Apparel Pattern & Grading Services
A pattern is created to produce prototypes or complete production runs. It is used throughout the production process. If there is no pattern the sample maker will have no direction. Patterns are the template of style and measurement. They communicate all necessary information to create perfect garments. Many call pattern makers the architects of the fashion industry.
Just as an architect creates blueprints used to construct sturdy buildings, pattern makers create patterns that are passed off to cutters and sample makers that are then used to create well-constructed garments. Without blueprints contractors would have no way of knowing where to begin and where to end. The original design intended for the building could end up being entirely lost and the building itself could risk being deemed unsafe or even worse… collapse.
Without patterns the original design will be lost, and garments will be structurally unsound, ill-fitting, and ultimately unsellable.
Need to Know Information
To communicate properly with the pattern maker the designer should be prepared with the following:
How the finished garment should look;
Design, shape, fit, measurements and placement of all details for each garment.
The pattern maker works with this provided information, along with front and back sketches, technical flats, and spec sheets. All details from width of pant leg, spacing between pleats, special linings, specific types of seams, etc. are needed to expedite the completion of each pattern and garment/product.
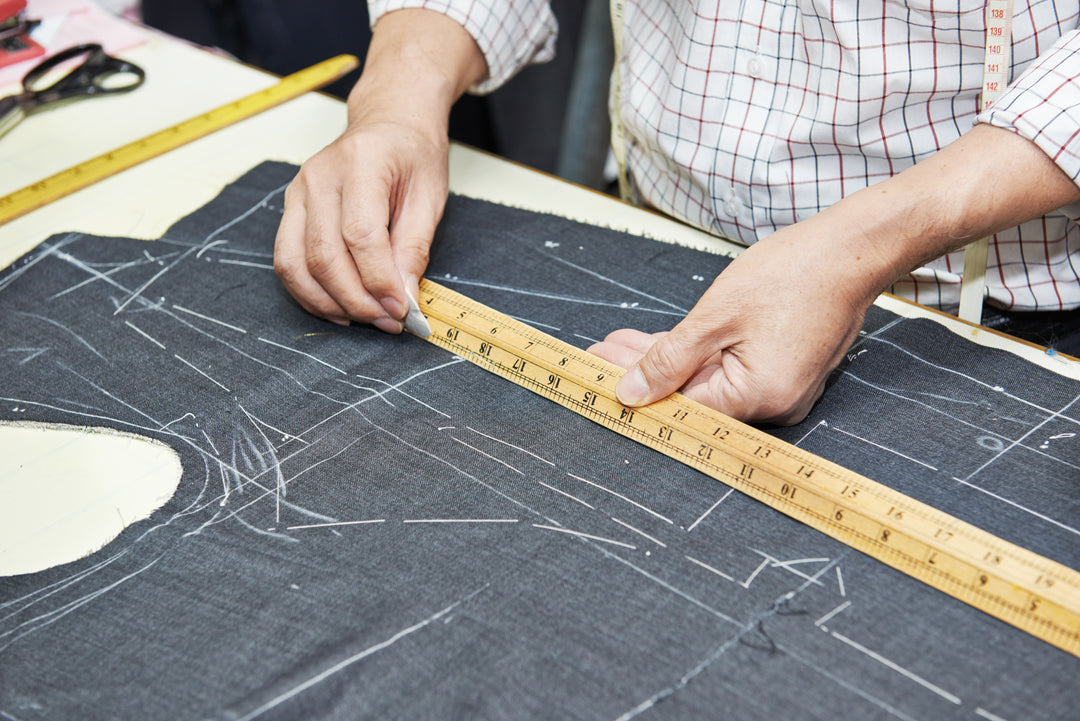
Pricing
Starting base price for any pattern is $150 which includes up to 5 pieces. Each additional piece needed for the garment is $15 each.
- We consider a typical t-shirt to consist of 5 pieces; Front, Back, Left Sleeve, Right Sleeve and Collar.
- A Hooded sweatshirt, for example, would consist of 10 pieces; Front, Back, Waistband, Left Sleeve, Right Sleeve, Left Cuff, Right Cuff, Front Pocket, Left Hood, Right Hood.
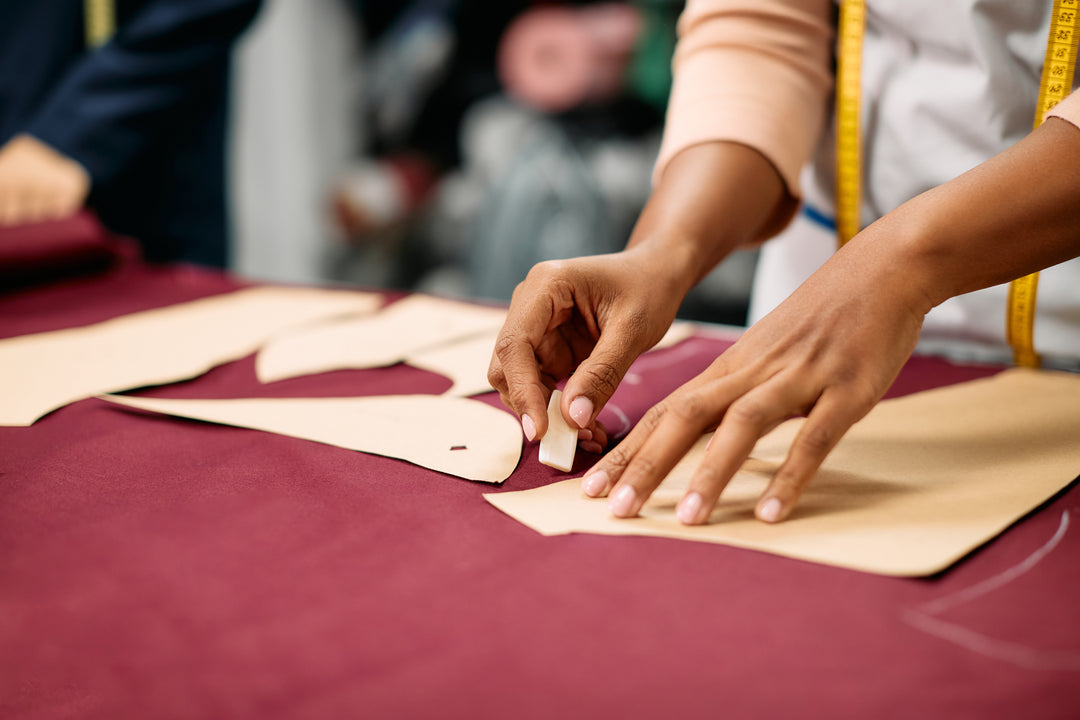
How Does Pattern Making Work?
Creating a precise pattern is very important in cut and sew manufacturing.
The process begins by draping on a form or drafting from a basic sloper flat on a pattern drafting table. From this step several rounds of adjustments are made. Pattern makers repeatedly measure, mark, re-measure and re-mark until all fit needs/requirements are accomplished and all design/style lines are created. From the initial paper pattern, muslin is cut and sewn into the garment used in the first fitting.
Based on the designer’s feedback in regards to the garment/product shown in the first fitting, the pattern maker will then revisit the original pattern and make the adjustments necessary to perfect the pattern. From this second pattern a second fitting garment/product is cut and sewn and another fitting is conducted. Again the designer gives feedback and from this feedback final adjustments are made to the pattern.
Now, you’re ready to begin your SMS (Salesman Samples).
Grading
Patterns initially are made in only one size. In order to produce clothing that fits various body types and sizes, the pattern pieces must be increased or decreased geometrically to create a complete range of sizes. The process of re-sizing the initial pattern is called “grading.” Each company determines its own grade specifications for each size, and size specifications vary slightly from manufacturer to manufacturer.
There are no standard sample sizes in the garment or pattern industry. Each manufacturer sets its own base pattern measurements and grades patterns based on a specific customer base. Grades can differ between industries, companies, and even different product lines. This is why one size 8 can be different from another size 8 (i.e., different base pattern measurements) and why the difference between a size 8 and 10 can vary between two different companies.
Grades typically decrease or increase by an inch from size 0 to size 10; after that, from sizes 12 to 16, a decrease or increase of two inches between each size is customary. A “standard” industry grade, from Small to X-Large, is two-inch difference in circumference, with a half-inch length difference from one size to the next.
It’s important to remember that grading only makes a shape larger or smaller and isn’t intended to change a shape. Grading is also important because it isn’t enough to merely make everything equally larger or smaller. Instead, you must take into account proportional sizes of different body parts. One person’s waist can be vastly different from another person’s waist — but you won’t see anywhere near the same size variation in arm circumference.
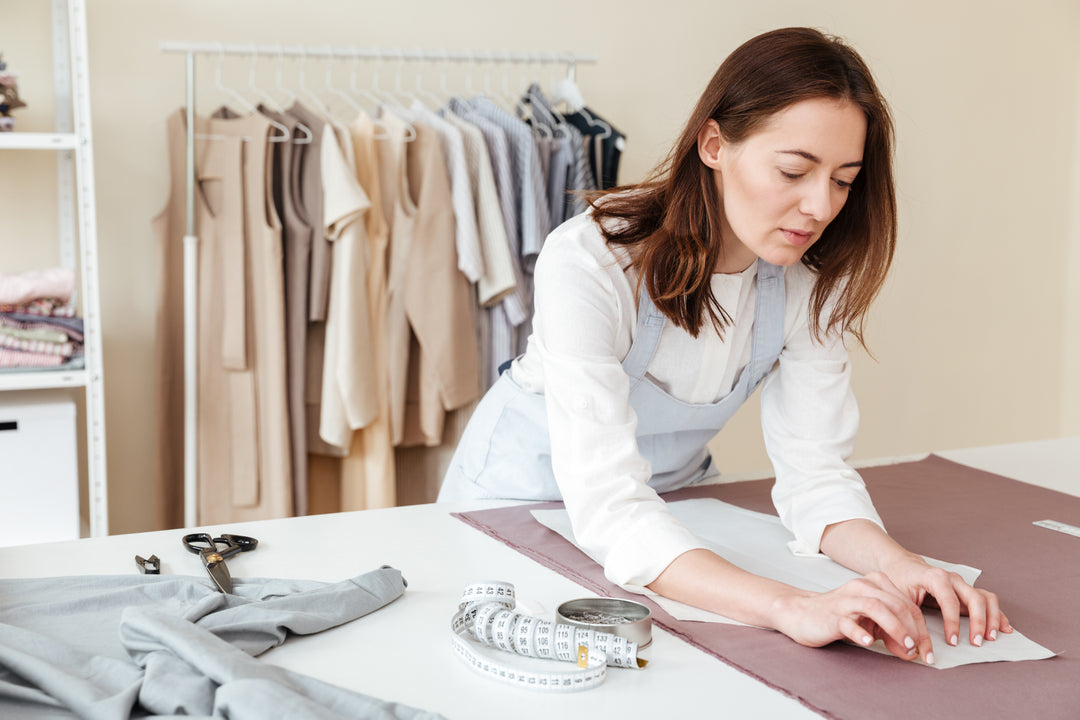
Garment patterns are incredibly important in cut and sew manufacturing.
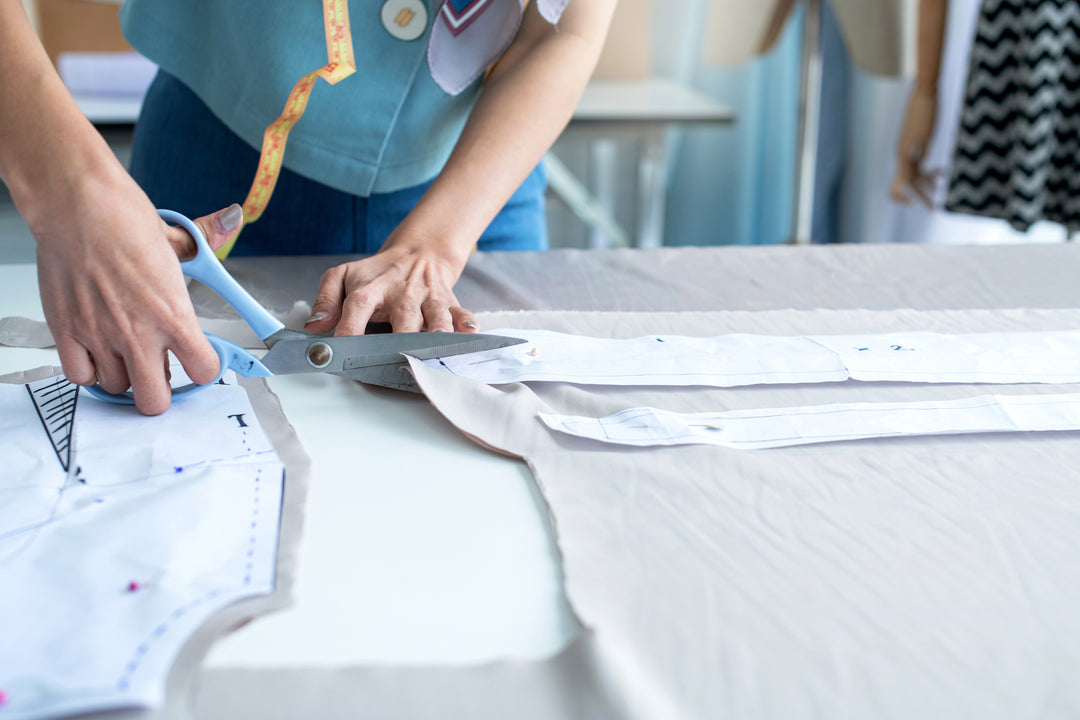
Creating a precise pattern is very important in cut and sew manufacturing.
Grading a cut and sew pattern allows the producer to create different sizes of the same garment.
Other Services
- Dye Sublimation Printing
- Blank Apparel Sublimation Printing
- Cut & Sew Dye-Sublimation
- Screen Printing
- Standard Plastisol
- Water Based & Discharge
- Foil Printing
- Specialty Inks
- Woven Fabric Labels
- Embroidery
- Direct Embroidery
- 3D Puff Embroidery
- Tackle Twill & Applique
- Patches
- Custom Cut & Sew Manufacturing
- Pattern & Grading
- Sampling & Production
Clothing Pattern Making & Grading
Clothing Pattern Making: The Foundation of Fashion Design
Understanding Clothing Pattern Making
Clothing pattern making is essential for creating well-fitted garments. It involves designing patterns that are tailored to specific body shapes and sizes. Because every person has unique proportions, designers need to understand how fabric drapes and moves. This knowledge allows them to create patterns that not only fit but also enhance a person's silhouette. However, mastering this skill takes time and practice, so patience is key.
The Role of Technology in Pattern Making & Grading
Although traditional methods of pattern making are still widely used, technology plays an increasingly important role. Software programs help streamline the process by allowing designers to make precise adjustments quickly. This means that patterns can be graded and resized more efficiently. But it’s important to remember that technology should complement, not replace, the designer’s creativity and expertise. So, combining both approaches often leads to better results.
Tips for Beginners in Pattern Making
If you're new to clothing pattern making, start with simple projects and gradually work your way up to more complex designs. You’ll find that practicing regularly improves your skills significantly. Additionally, invest in quality tools like rulers, tracing paper, and scissors because they make the process smoother. Because mistakes are part of learning, don’t get discouraged if things don’t turn out perfectly at first. Instead, focus on improving each time.